Rotomolding Design
Brief Rotomolding History
In terms of modern plastics, Rotational Molding is often regarded as one of the more recently recognized manufacturing processes. Rotational molding was developed in the late 19th century to develop the production of hollow vessels, particularly metal artillery shells. In the first part of the 20th century, the process was used to mass produce hollow chocolate eggs. By the 1920's, plaster of Paris was being molded by a means of biaxial rotation. Plastic materials were developed in the 1950's for use in the rotomolding process. One of the first major applications for the Rotational Molding process at the time was to produce doll heads from a liquid PVC plastisol material. By the 1980's a wide variety of materials had been developed for the Rotomolding industry.
Rotomolding Design
Innovation, Strength, Durability
Rotational Molding, like all additional plastics processing techniques, has its very own distinct conveniences, downsides and part-design needs. A designer of rotationally molded parts needs to recognize that there are no stresses or pressures involved that directly press the plastics thru the mold, as is the instance with thermoforming, injection and blow-molding. In rotational molding, the mold spins with a pool of liquid or powdered plastic and the plastic adheres to the scorching surfaces of the cavity to develop up the preferred wall thickness.
The ideal design for a rotationally molded part is any hollow shape where several aspects in the part design are smoothly blended from one shape to the next. The smooth blending of shapes results in a final product that has increased strength and is easier to produce and as a result, more economical. The successful design of any plastic product is dependent to some extent at least, on proportioning the style of the component to accommodate the particular product that is to be made use of.
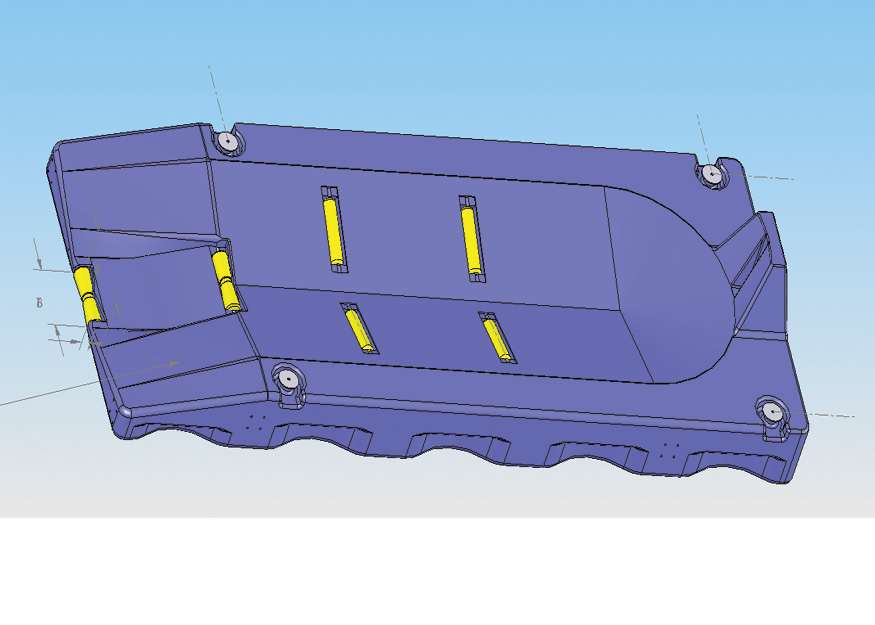
A rigid, low-mold shrinkage, high-temperature, hard-flow, amorphous component such as crystalline polyethylene is commonly used in Rotational Molding. Each plastic component has its own unique design requirements. This process is superior in many ways which is why it sees continual growth. Much of this growth is due to material conversions from less durable materials to rotationally molded Polyethylene which is more durable and has a longer lifespan than most materials available.
The design team at Granger Plastics has the experience you need to determine what design elements are necessary to produce your product as efficiently as possible. Use our experience in creating excellent rotational molding designs and manufacturing parts that are of the most superior quality.
![]() |
Rotomolding Design Links
Granger Plastics Rotational Molding Info
For more information on Granger Plastics Rotational Molding: Click Below
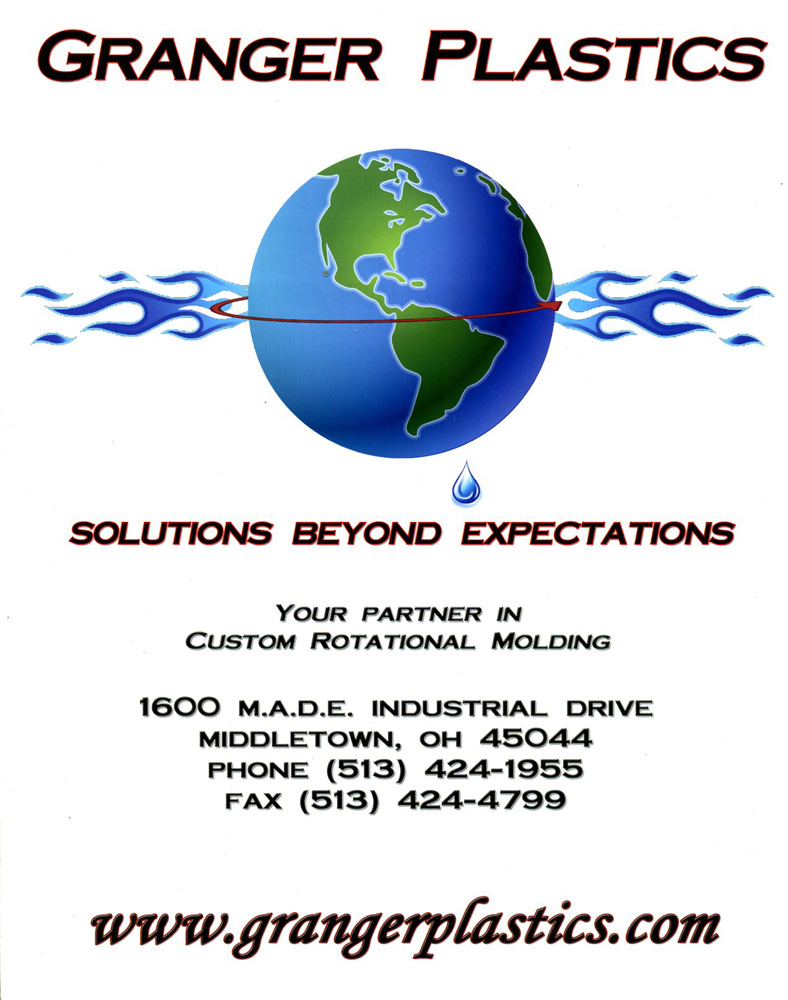